Here are some detail pictures from last week that I thought were interesting.
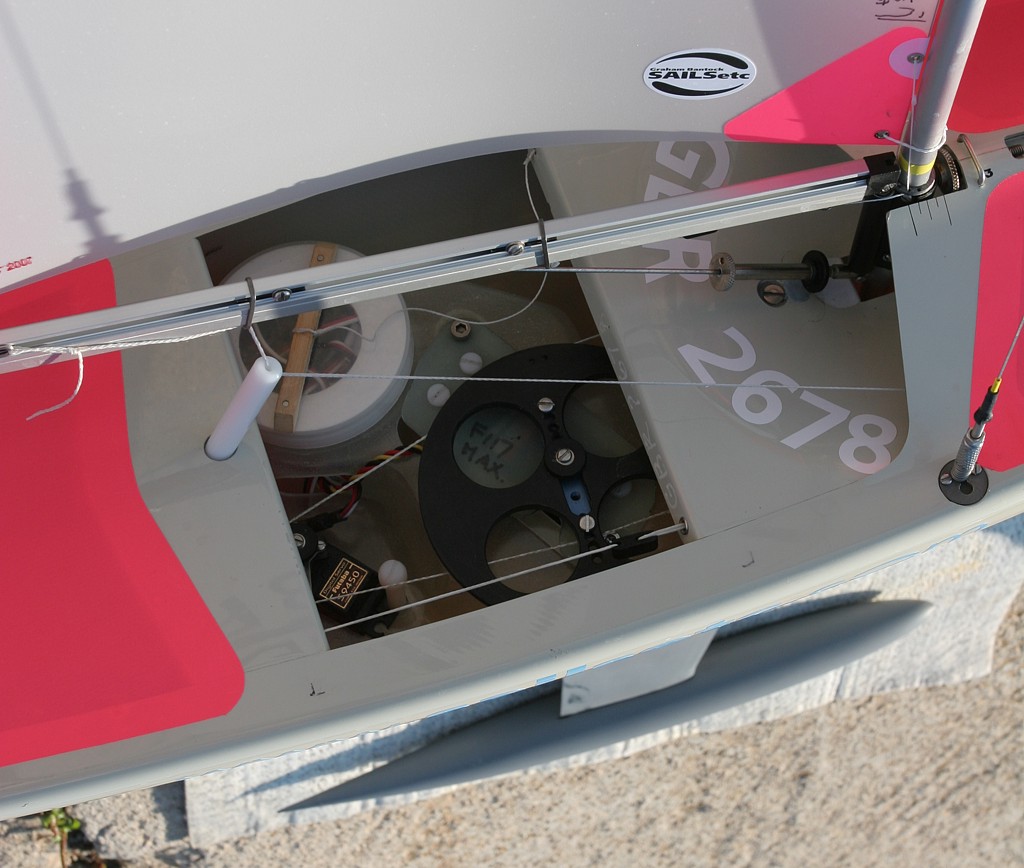
Graham Bantock's Topiko. Note quick-release bottlescrew and deck-fitting far right. Also note how the cunningham is threaded through a plate with holes around the mast. I think this gives a variable cunningham tension (tight on the beat, looser on the run?)
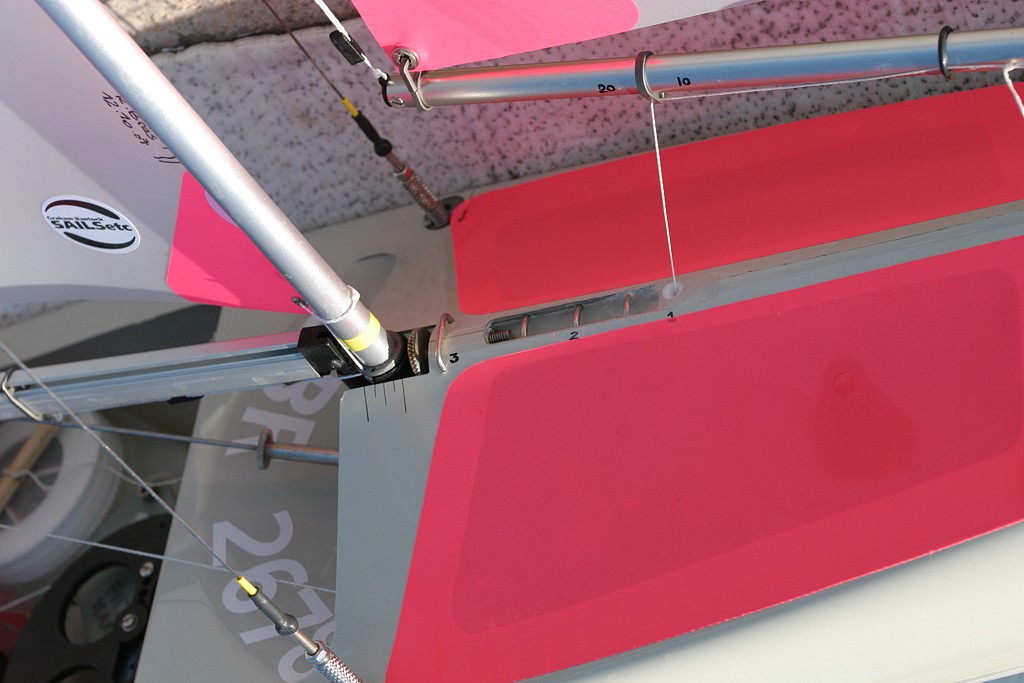
Recessed jib-sheeting hooks. With the new sheeting system and the arm-winch configuration there's no endless-loop or other sheeting lines on the deck. Just the jib sheet very neatly coming out of a PTFE fitting in the foredeck. Many boats do not use a separate sheeting position for the no2 and no3 rigs, so I guess threading the sheet under the metal wires for the no2 and no3 rigs is optional.

Same kind of recessed wire-hooks for no2 and n3 rigs. The no1 rig uses a piece of Dyneema that attaches to the bottom of the boat and comes up on foredeck through a tube. I wonder if the added complexity for building this is worth it? Sheeting angle adjustable with a bowsie.
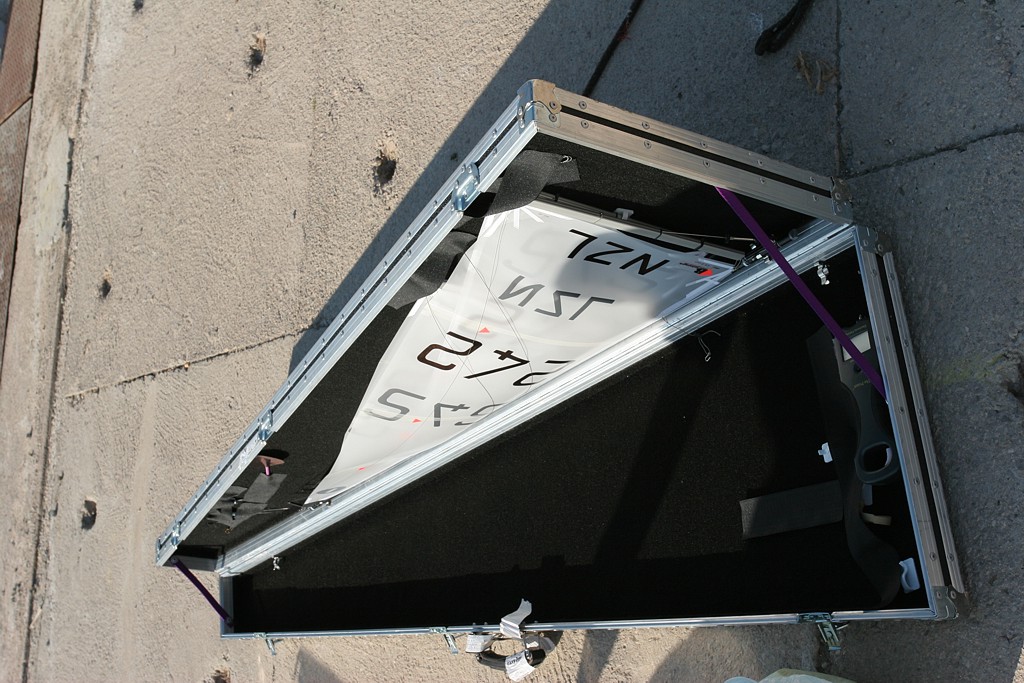
John McPherson's very serious looking rigbox. My own is similar but this one is deeper so could probably fit two sets of rigs.
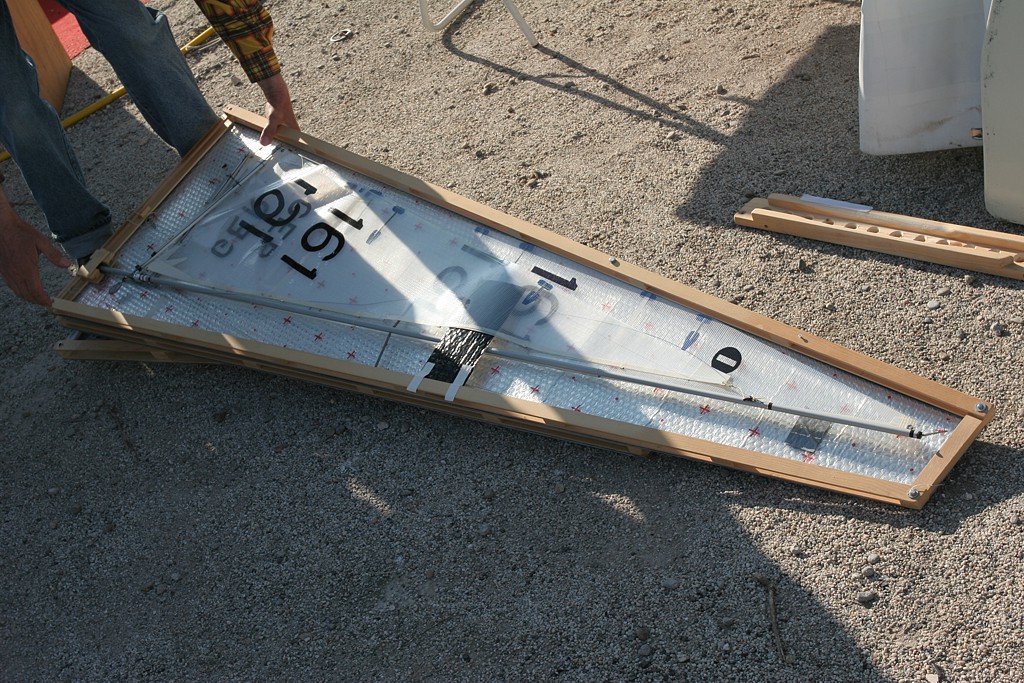
A Gearman, breathing version of a rigbox.
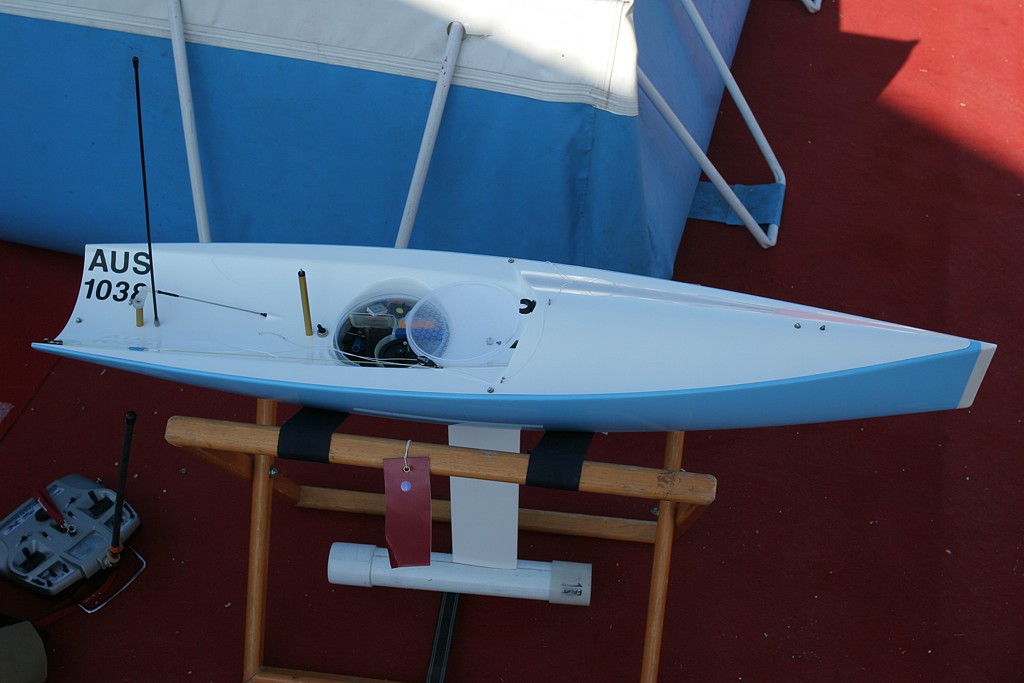
Craig Smith sailed the same Obsession prototype that he won with in Mooloolaba, and Simon Kellet's Obsession boat pictured here is the first (and so far the only!) production boat.
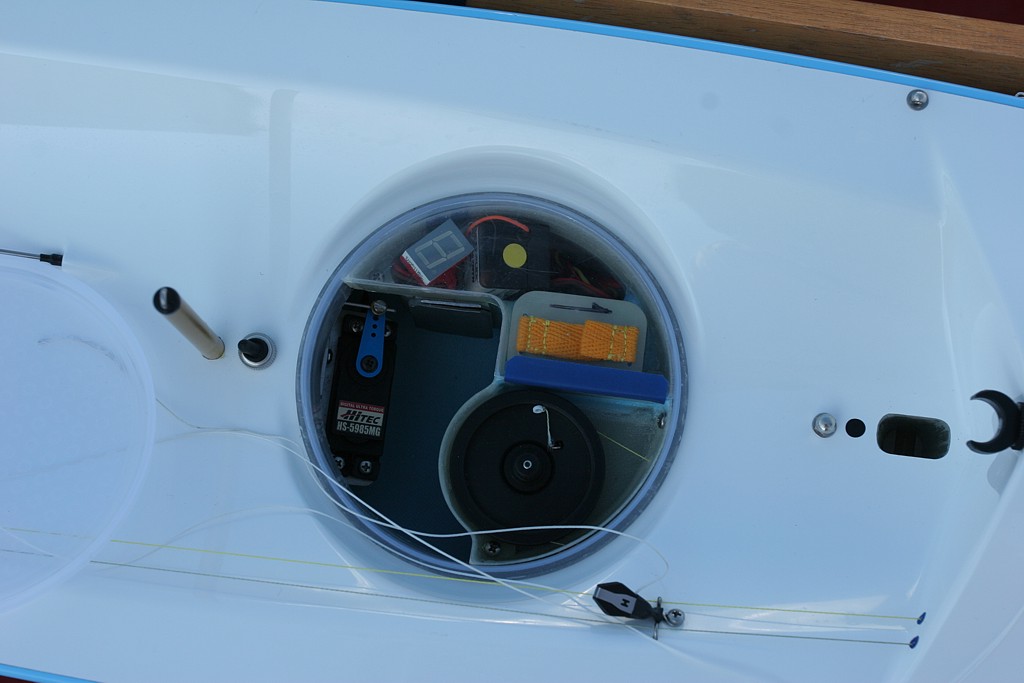
The round Decor hatch with all the radio installations neatly in one place. The battery even has connectors on the bottom of the fibreglass casing - just press it down and it connects.
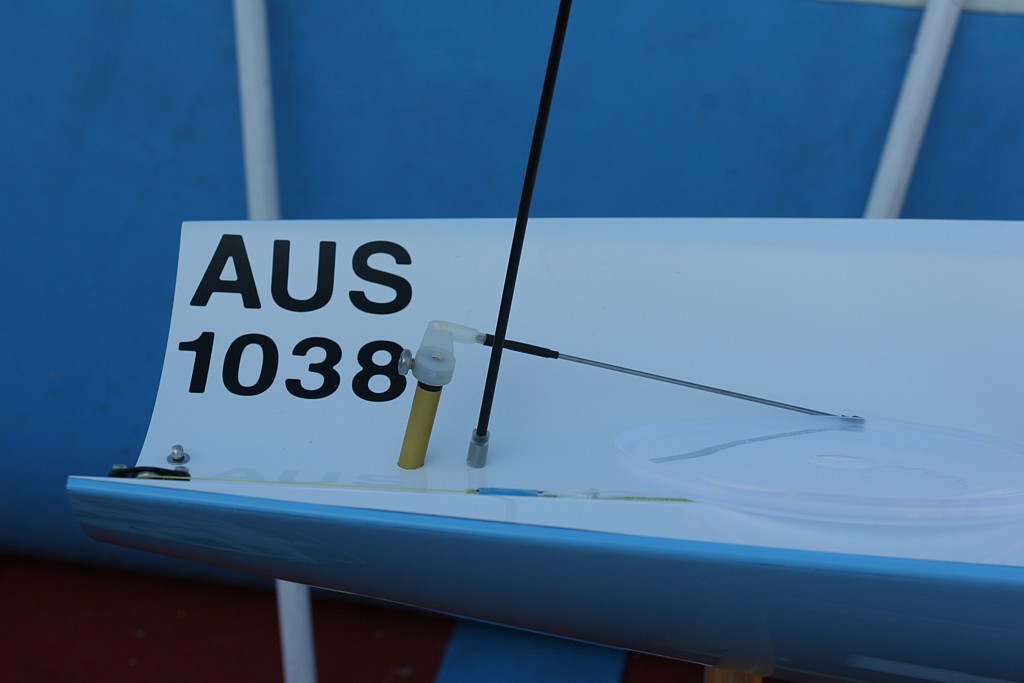
Note how much the rudder tube leans forward. I wonder what this does to the function of the rudder. Any boat designers want to comment below?
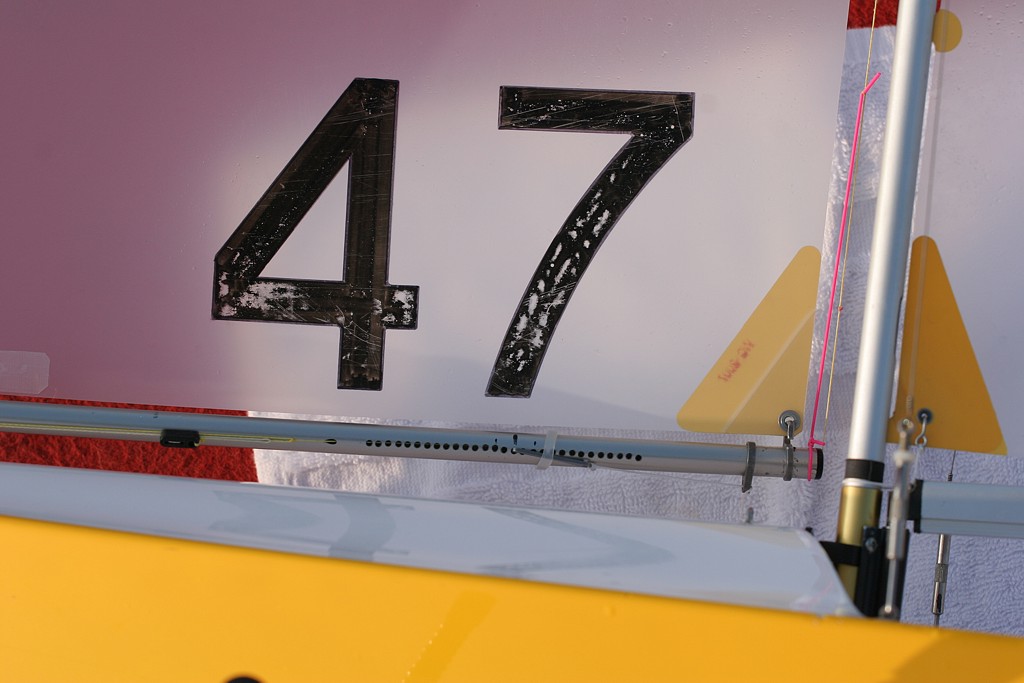
Craig Smith's no1 rig jib. Note how the topping lift bowsie is to the left in the picture and the topping lift is threaded inside the boom and comes out at the end. The pink elastic keeps the topping lift tight so it doesn't catch the spreaders. There's only one sheeting eye in the deck that is used with all three rigs. Similar to GBR-95, the cunningham is threaded around the mast to give an auto-adjusting effect. Lester Gilbert has two interesting notes on auto-adjusting cunninghams here and here.
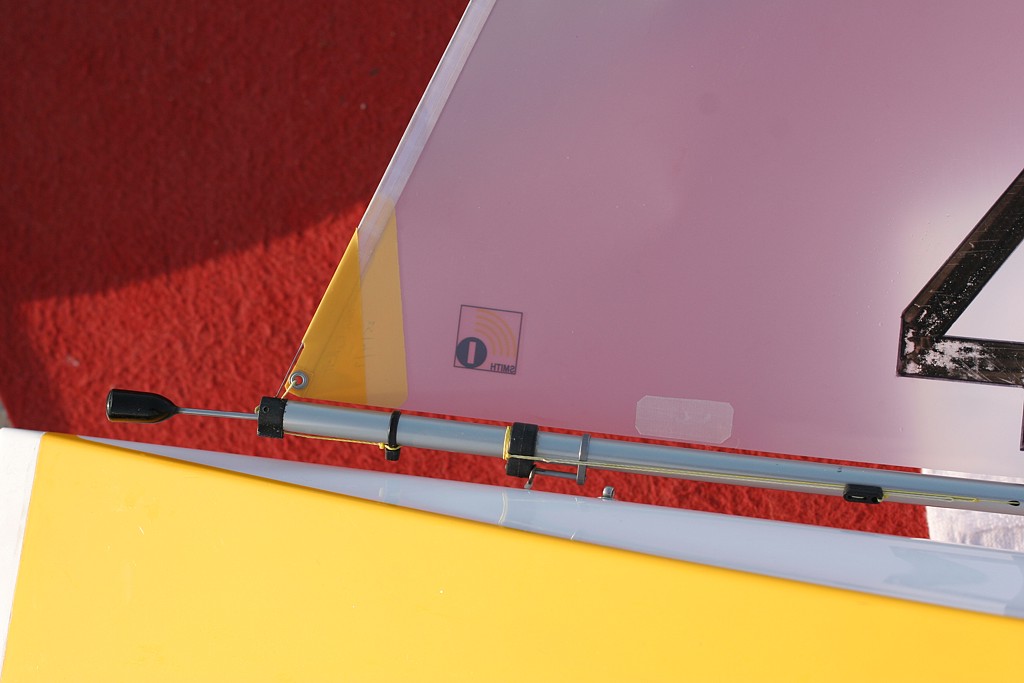
Forward end of Craig Smith's no1 jib. Craig is also using the Dyneema thread idea for the no1 rig jib swivel. Although putting in the tube is one more job when building the boat you do get a useful stiffening of the foredeck at the same time. Craig seems to use the same deck-eye for both the no2 and no3 rigs as there is only one attachment point aft of the no1-rig swivel.
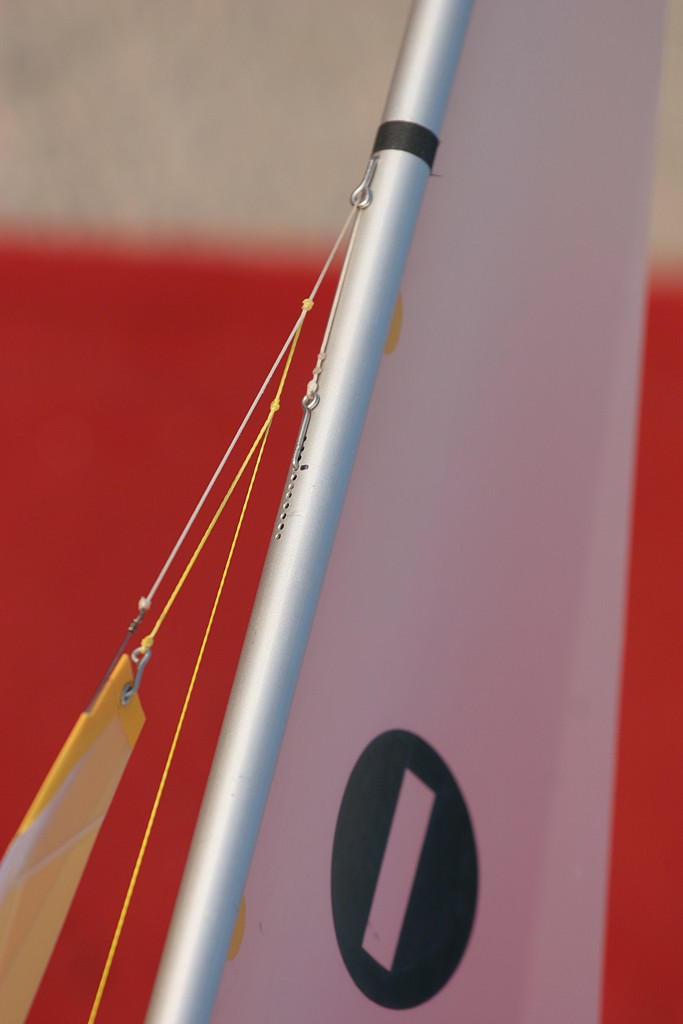
Craig's very neat and minimal top jib attachment. The overall rake of the mast can be adjusted by moving the hook up and down on the mast. Note how the topping lift and the jib attach to the jibstay. There's no shroud attachment point in sight in this picture (compare that to pictures below) - which means Craig uses a much lower attachment point than Graham.
I'd love it if someone took measurements and wrote them up like I did in 2003.
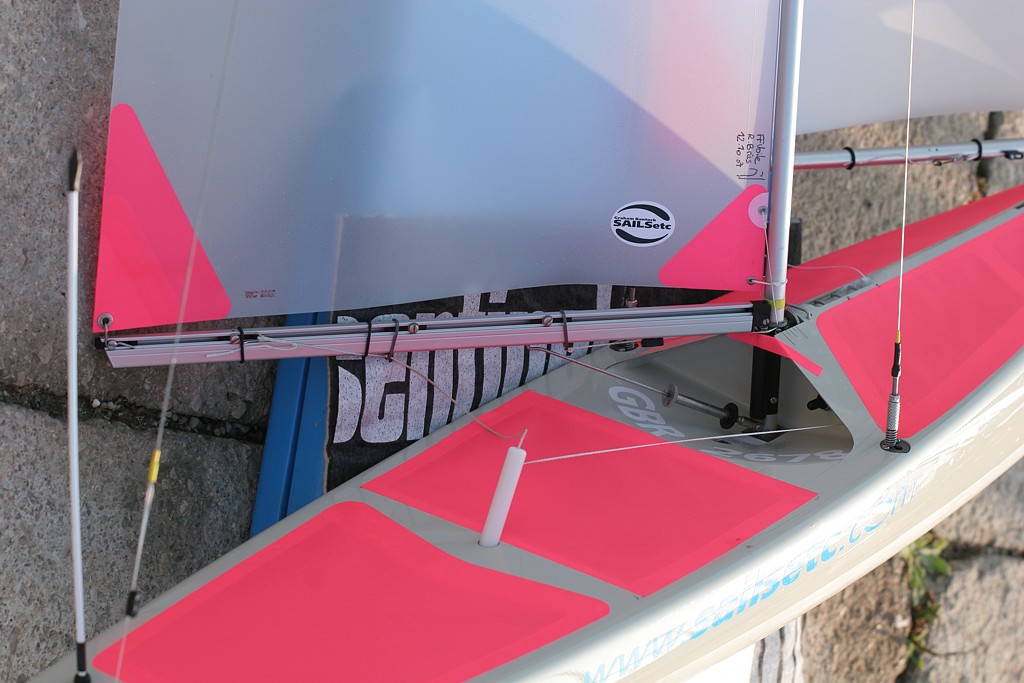
Graham's boat again with another view of the new quick-release bottlescrew. Note that Graham doesn't use adjustable sheeting attachments any more. I think it's because the arm-winch is significantly more precise than a drum winch, so there is not much variability from day to day or month to month in how far the sails come in when you set up the boat.
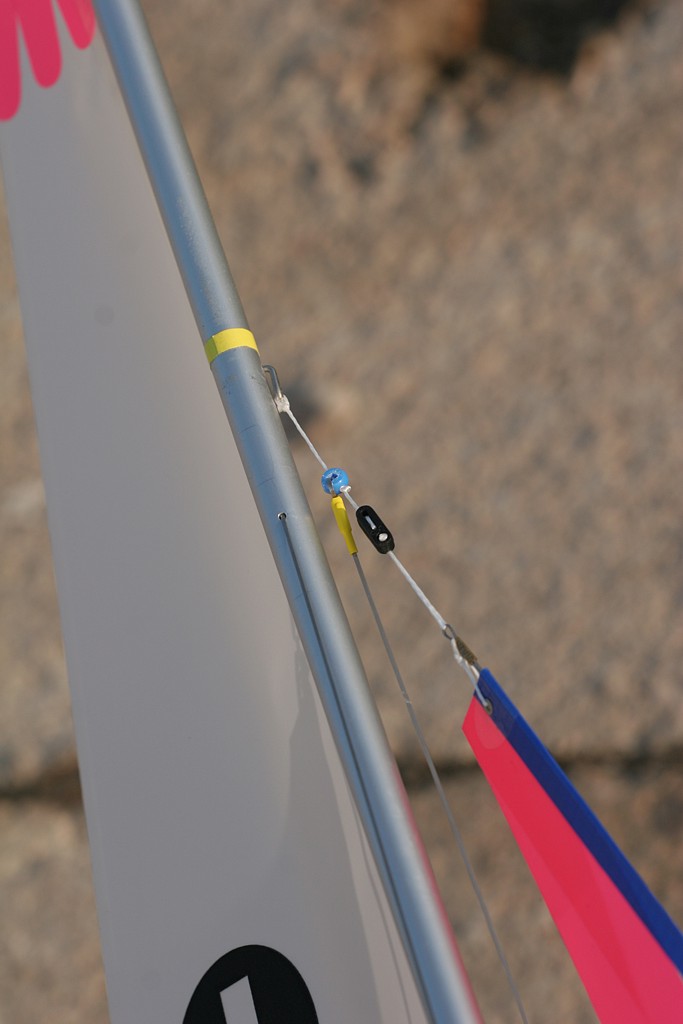
Graham's top jib attachment with a bowsie for controlling mast rake. Note use of the flat steel tape for the topping lift. The same steel tape is used for the shrouds, which attach just below the jib-attachment point. Compare this to Graham's Mooloolaba boat where the shrouds both attached to the same point on the front side of the mast. (more from Mooloolaba here)
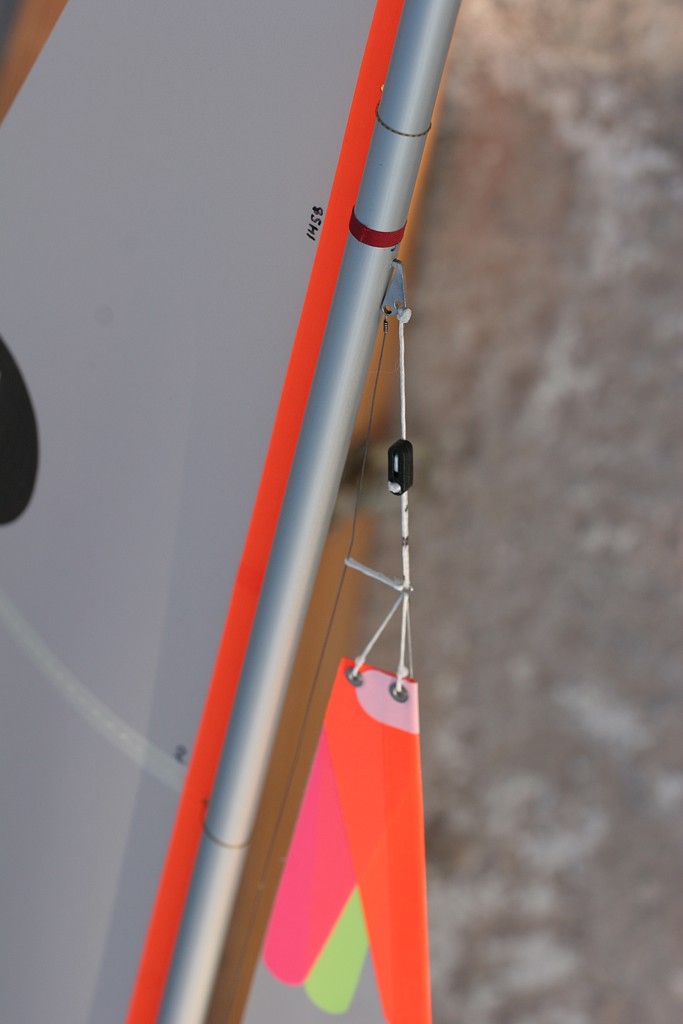
Brad Gibson's no1 rig jib with a nice cnc-laser-cut steel hook for the jibstay and the toppinglift, and a piece of string pulling the topping-lift forward and clear of the spreaders. Again no shroud attachment point in sight - which must mean that Brad uses a similar low-shrouds configuration as Craig.
I have some more of these which I'm hoping to get online soon, in particular some pictures of the Lintel and more cnc-laser-cut fittings from David Potter.
If anyone has some pictures that they think would be a good addition please feel free to comment below or email me directly!