Jari sent me some pictures of tiller arms that he machined during the weekend.
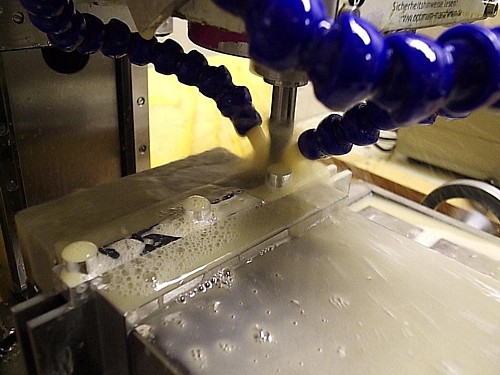
These parts need to be machined in three separate stages, here's stage 1 where the tillers are first roughed and then finish milled.
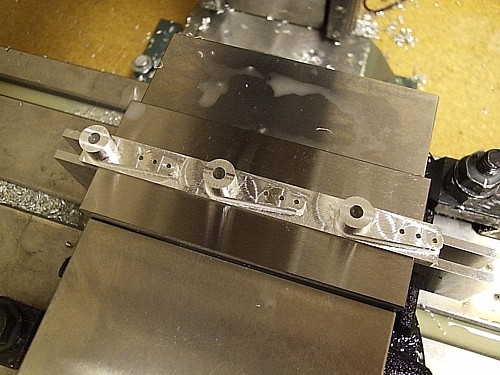
Here's what the parts look like after the first stage. After finishing the hole for the axle and three holes for the push-rod are drilled. In stage two the parts are turned 90 degrees and fixed using a jig. A hole can then be drilled and tapped for a set-screw that will tighten against the rudder axle.
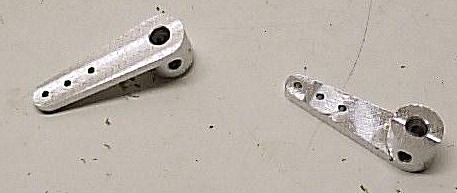
In stage three the whole thing is flipped over and the bottom of the stock material is machined off, which results in these completed parts.
These are still prototypes, for the Noux Mk2 I'd like to see two things: (1) assembly of the boat without tools, i.e. the attachment of the tiller arm to the rudder axle should not require any special tools (allen key, screw driver, etc.). This could be achieved with the current design simply by using a screw with a thumwheel. (2) a fixed relative position between tiller and rudder axle, i.e. when I attach the rudder I want to be sure it sits straight without having to check it everytime and possibly re-trim on the transmitter. A low-tech solution is to file or grind a flat part on the rudder axle onto which the set-screw pushes. If anyone has better ideas I'd be glad to hear about them !
Update 2006 Dec 05:
Johan Prak from the Netherlands sent me a picture of his homemade rudder fitting. A very simple design that anyone can make:
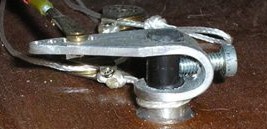