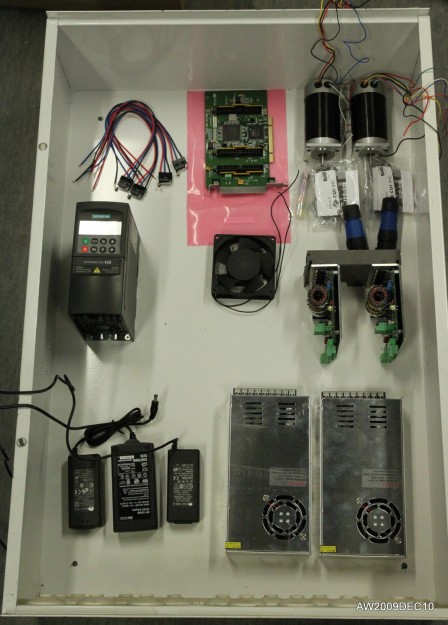
Most of the electronics I've ordered for the lathe has arrived by now. Still waiting for the servo-drive for the main spindle.
Bottom left are three switched-mode power supplies: 5V 3.5A (logic etc), 12V 3.3A (brushless amps, E-stop chain, etc), 24V 1.3A (spindle brake)
Bottom right are two Chinese 350W 48VDC 7.3A power supplies for the X- and Z- servos. Bought on e-bay from one of the Chinese sellers that has free worldwide shipping, and these were not caught by the local customs, so I paid around 28 euros/supply!
Mid row: on the left a Siemens Micromaster 420 0.37 kW VFD which will be used for a future live-tool spindle, and on the right two pico-systems brushless servo-amps.
Top: limit switches, Mesa 5I20 PCI-card, 180W Brushless servos for X and Z, CUI encoders, Amphenol connectors.